Silicone antifoam
Silicone antifoam:
When a gas is dispersed and stabilized in a liquid, foam forms. If not foaming, the bubbles can grow rapidly and cause problems in the system that either greatly increase the volume of the product or create problems in the production process.
Foam typically occurs during the process of mechanical mixing or stirring, mixing, distillation, fermentation, filtration and filling. While mechanical processes can control the floor, chemical agents are more diverse, more efficient, and more economical. Using foam is one of the easiest ways to remove foam. In fact, it disperses or disperses easily, leaves no significant residue and odor, and meets the relevant regulatory requirements.
Silicone foams, or essentially the same as silicone antifoams, are based on silicone polymers. These are produced in the form of oils or water-based emulsions. The silicon compound contains a hydrophobic silica dispersed in silicon oil. This silicone antifoam consists of the dispersion or dispersion of a hydrophobic silica in silicone oil. In order to ensure the stability and dispersion of silicon, emulsifiers are added to this compound, these emulsifiers contain silicon glycols and other silicone compounds.
Foam control is a major issue for manufacturers in many industries. They use high-performance minerals to make anti-foam formulations. Silicone antifoams have the highest performance efficiency in various industries and floor control systems.
These floor mats are among the most widely used and heavy-duty defomers. Because they have a very good performance in both hitting the floor and releasing the submerged air.
Types of silicone foam
If we want to classify silicone flooring in terms of chemical nature, we see that it is divided into two categories:
Liquid silicone antifoam
Silicone powder antifoam
Powdered antifoams are essentially oil repellents on a particle carrier such as silica. These are added to powder products such as cement, gypsum and detergents.
Specifications of silicone antifoam:
Silicone foam is a viscous and milky liquid that has a neutral ionic charge and is made of polysiloxane compounds.
Performance of silicone antifoam:
Silicone anti foams act very quickly and remove the film consisting of foam that is on the liquid surface. The low surface tension of the anti-foam droplets causes the silicon to flow continuously in the adjacent floor films and prevents the re-formation of foam on the surface.
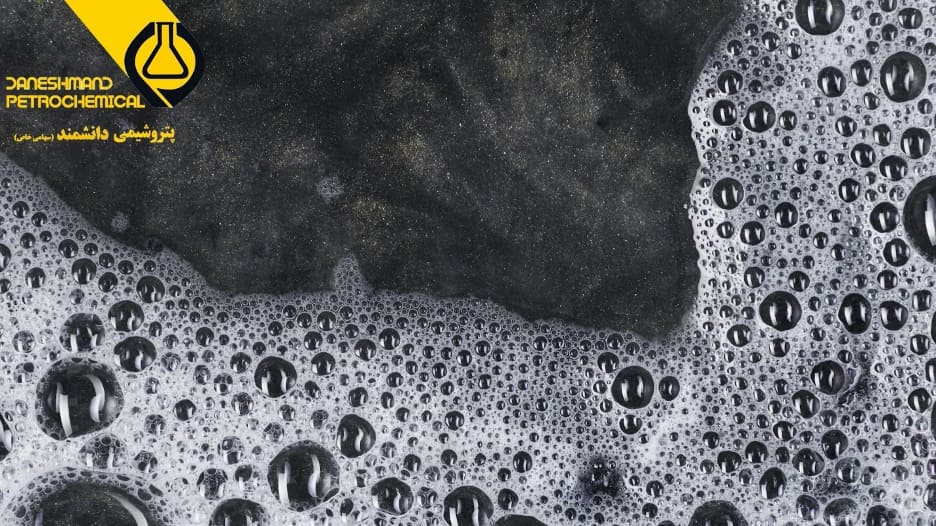
Advantages of using silicone foam:
Silicone foam foam is optimally used in all industries due to its formulation. Silicone foam foam can work in harsh conditions such as high temperature and high acidity. It is important to know that silicone foam foam does not cause corrosion and is very safe. Another important point is very low consumption. These are anti-foam and their work speed and of course the reasonable price of this type of anti-foam put them in a special place.
Application of silicone anti foam:
Silicone antifoam is used in various industries. Fluorosilicon-based foam may also be suitable for very specific applications. Among their uses, the following can be mentioned:
Oil and gas and petrochemicals
Excavation
Production of emulsion resins
Textile
Pharmacology
Food industry
Agricultural pesticides
Detergent and cleaning industries
Crude oil and oil refining
Wastewater treatment units
Paper making
Paints and coatings industries
Textile and leather industry
Production of auto parts and accessories
chemical industry
Crop protection
Making pulp
Application of silicone foam in paper making and wood industry:
In the early 1990s, silicone antifoam emulsion, which reduced surface roughness, was used in the wood pulp and paper industry. Which reduces BOD in wastewater sediments.
Application of silicone flooring in the construction and concrete industry:
Silicone antifoam is used in concrete casting materials to create stone columns, wall arches or other decorative pieces to prevent bubbles.
In many cases, polyurethane and latex materials are used in the concrete casting process. These materials have a high and contradictory shrinkage surface that causes foam in the product. Silicone antifoam has low shrinkage.
Polyurethane and latex materials not only shrink during the manufacturing process, but also have no pigment. The color of the stone is very important because the first stone produced must match the thousandth stone produced. When using concrete to make artificial stone, silicone is a great solution for paint pigments because it is hydrophobic. The pigments used in concrete have water, so the pigments are easily sent in the form of silicon.
Anti-foam application in cement industry:
Cementing of oil well wall pipes is a very important and necessary thing in the oil industry that must be done with the highest quality. One of the factors reducing the quality and strength of cement is the formation of gas bubbles (foam) in its mass. Therefore, in addition to the presence of anti-foam for drilling in mud, this material is also used in drilling cement. Of the various types of flooring available, silicone flooring is the most widely used and approved in the industry.
Anti-foam application in oil, gas, petrochemical and drilling industries:
In the drilling industry of oil wells, we have to use drilling mud for two reasons. The first reason is to move the drill bit and increase the efficiency of the drill. The second reason is the high pressure difference between the end of the well and the beginning of the well in drilling oil wells. This difference will cause the eruption of fluids inside the formation to the surface and to prevent the eruption of these wells, the presence of drilling mud inside the well is required. The weight of the drilling mud does not allow fluids to return to the surface, but if foam forms in it, it will lighten and lose its properties. Therefore, the use of anti-foam for drilling mud prevents the eruption of wells and the occurrence of financial and human losses. The oil coming out of the well contains gas and water. When separating oil from gas in the separators of operating plants, the joint surface of gas and oil is prone to foam formation. The formation of foam reduces the separation efficiency on the one hand and increases the liquids associated with the separated gas on the other hand. Therefore, it is necessary to use a suitable foam. Silicone flooring is currently used in factories.